-
Automatic Bread Production Line
-
Automatic Cake Production Line
-
Automatic Toast Production Line
-
Cookie Production Line
-
Bakery Tunnel Oven
-
Baking Cooling Towers
-
Bread Proofer
-
Depanner
-
Flat Bread Production Line
-
Granola Production Line
-
Cake Depositor
-
Food Industry Conveyors
-
Baking Pan Handling Equipment
-
Rotary Rack Oven
-
Cookie Depositor
Independent Controlled Gas Bakery Tunnel Oven With SEW Motor
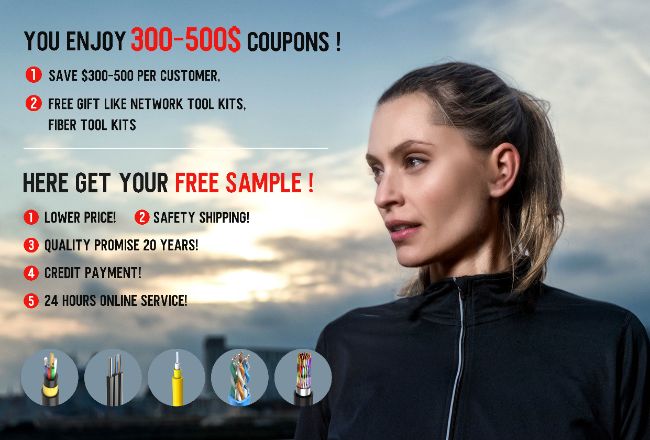
Contact me for free samples and coupons.
WhatsApp:0086 18588475571
Wechat: 0086 18588475571
Skype: sales10@aixton.com
If you have any concern, we provide 24-hour online help.
xVoltage | 220V/380V | Condition | New |
---|---|---|---|
Application | Cakes,breads, Cookies | Material | 304 Stainless Steel |
Motor | SEW | After-sales Service Provided | Engineers Available To Service Machinery Overseas,Field Installation,commissioning And Training,Free Spare Parts,Online Support |
Highlight | 1050mm Bakery Tunnel Oven,SEW Motor Bakery Tunnel Oven,304 Stainless Steel Tunnel Baking Oven |
Saimai is one of the manufacturers of tunnel ovens, our tunnel ovens range in working widths from 1050mm to 3300mm and can be configured for virtually any type of product. Our experience in tunnel oven technology allows us to design and commission the optimum baking solution for our clients. We offer heating systems that include, convection (indirect-heated), direct gas-fired and hybrid methods.
Baking chamber width | 1050mm-3200mm |
Baking chamber length | To be customized |
Baking conveyors | Slat band plate, Mesh wire conveyor, Steel band |
Conveyor load capacity | Up to 40Kg/m2 |
Baking time control | Ratio up to 1:10 |
Modular design | Pre-assembled, fully insulated, pre-wired |
Heat resource | NG,LPG |
In order to directly transfer heat to the products, direct gas fired ovens use ribbon burners that are placed above and below conveyor belts, the flames created by each burner then radiate energy into the baking chamber, heating the air and the products.
Each burner is supplied with a mixture of gas and air. The pressure of this mixture determines the extent of the combustion reaction (power delivered), and hence the temperature set point of the oven.
There are various arrangements for adjusting the size of the flame across the width of the oven to ensure even heating across the band.
Bsed on the standard oven,we have improved the control system and ignition system of new type oven, with the features as following:
Air supply system | Each zone is equipped with an independent air supply system. |
Gas supply system
|
Each zone is equipped with an independent gas supply system and equipped with the dual electromagnetic slow-opening valves can prevent the sudden connection of the gas |
Exhausting system | It is equipped with two sets of exhaust dampers respectively at upper and lower of each zone, Each exhaust fan is equipped with independent inverter, and the exhaust volume can be adjusted in real time. |
Ignition system
|
It is automatically controlled by the burning program controller, and each burning pipe can be selected and turned on/off from the touch screen, Flame detection ensures gas is cut off when there is no flame in the combustion system. |
Temp Control system
|
Three temperature probes are set for the upper fire in each temperature zone, another three temperature probes are set for the bottom fire, and the average value of the three temperature measurement points is taken as the reference temperature, to reduce the measurement error and improve the temperature control accuracy. |
Control system | The core control system is Rockwell PLC, and the distributed IO control method is used to realize regional modular control. The main control module is used to control the overall operation of the system; each zone is equipped with independent temperature control modules to achieve precise control; The whole oven is equipped with multiple safety monitoring systems to ensure the safety and stability of equipment operation. |
our workshop :
Packaging and delivery :