-
Automatic Bread Production Line
-
Automatic Cake Production Line
-
Automatic Toast Production Line
-
Cookie Production Line
-
Bakery Tunnel Oven
-
Baking Cooling Towers
-
Bread Proofer
-
Depanner
-
Flat Bread Production Line
-
Granola Production Line
-
Cake Depositor
-
Food Industry Conveyors
-
Baking Pan Handling Equipment
-
Rotary Rack Oven
-
Cookie Depositor
Automatic Direct Fired Hotdog Roll And Burger Bun Industrial Production Line
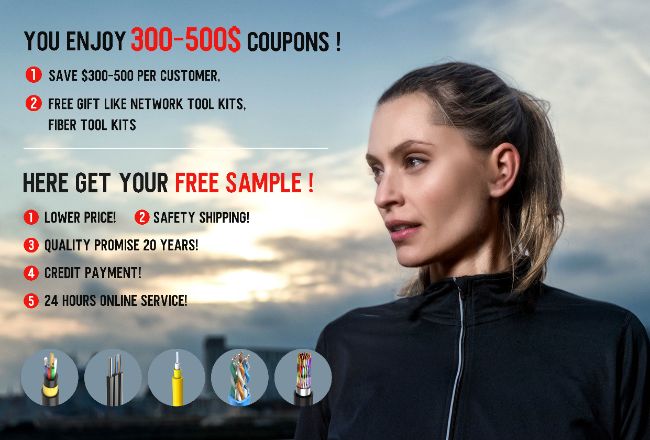
Contact me for free samples and coupons.
WhatsApp:0086 18588475571
Wechat: 0086 18588475571
Skype: sales10@aixton.com
If you have any concern, we provide 24-hour online help.
xVoltage | 220V/380Volt | Material | 304SS |
---|---|---|---|
Condition | New | Motor | SIEMENS,SEW |
Application | 12000-24000pcs Hotdog And Burger Bun Making Machine | Warranty | 1 Year |
After-sales Service Provided | Engineers Available To Service Machinery Overseas,Field Installation,commissioning And Training,Free Spare Parts,Online Support | ||
Highlight | ISO Cookie Depositor Machine,220V Cookie Depositor Machine,Cookie Production Line 1.2M Width |
Industrial commercial production line rolls and buns line
The line is designed for hotdog roll and hamburger bun together,with the capacity from 12000pcs-36000pcs/h.
The line can be equipped with:
Make-up line
Automatic Step-proofer
Automatic Trolley Loader (optional)
Automatic Trolley Un- Loader (optional)
Topping machine
Tunnel Oven
Suction Depanner/ Needle Depanner
Pan cleaning machine
Edge pan cooler
Pan buffer(optional)
Spiral Cooler
Packaging machines
Proofing Room
Pans, trays can all be handled by the proofing room. Different tray types can be used as long as their outer dimensions are equal. The proofing room has several racks that consist of one or more levels, making the proofing time and capacity flexible without increasing the floor space.
The pans are fed into the proofer by conveyor and do not touch each other. Once a row is filled, it is lifted with an L-shape carrier. This process is repeated until the first dough has reached the top level. Then, the pans are moved out of the proofing room.
The proofing room is accommodated with a temperature and humidity control system and insulated housing.
Tunnel Oven
Integrated PLC Control System
- The core control system is the PLC by Rockwell Automation, Inc. which is an American provider of industrial automation components with the brand name Allen-Bradley.
- The PLC and the distributed IO control method is used to realize regional modular control.
- The main control module is used to control the overall operation of the system.
- Each zone is equipped with independent temperature control modules to achieve precise overall control.
- The whole oven is equipped with multiple safety monitoring systems to ensure the safety and stability of equipment operation.
No. | Parts Name | Origin / Brand | Descriptions & Functions |
1.1 |
Programmable Logic Controller (PLC) |
Rock-well U.S.A |
PLC is used to directly collect on-site temperature and control the temperature through internal programming. Different temperature control methods can be selected according to different products. The temperature accuracy is controlled at plus or minus 1 degree Celsius, and the dual goals of constant temperature and energy saving are achieved in temperature control. In addition, the signal is screened and processed by PLC, and the anti-interference is stronger, which truly realizes real-time adjustment and whole-process monitoring. It is also equipped with strict safety measures to prevent disoperation, safety detection, alarm indication, etc., and there are up to 300 groups of product baking parameter storage functions, which can pre-store processing information such as temperature and time for recall. |
1.2 |
I/O Modules |
Rock-well U.S.A |
Modular design lets you independently select the I/O, termination style, and network interface. Modules slide together for easy install and uninstall for easier maintenance Removable wiring system saves time and money during installation and troubleshooting Comprehensive diagnostics and configurable features makes POINT I/O™ easy to apply |
1.3 |
Human Machine Interface (HMI) |
Rock-well U.S.A |
AB large-screen touch human-machine interface, supporting AB hardware control system, the command compatibility is guaranteed, there is no problem of command coordination and conversion of different brands, and the system runs very stably |
1.4 | Inverter |
Rock-well U.S.A |
Baking time adjustment, safety protection, constant temperature and over temperature, purification and exhaust air treatment. The whole system is equipped with 6-8 set of inverters. |
1: The oven is constructed gas-tight baking tunnel, divided into 2m/ section. Each section is connected on a frame, with a gas-tight connection between the sections.
2: the baking tunnel is insulated with 20CM-25CM layer of high-quality insulation material, in order to reduce heat loss to a minimum.
3. Inspection door on the control side
4. Stainless steel side and top outside panel.
5. The temperature is measured in each zone, both temperature underneath and above the product to be baked. PT-100 sensors are fitted in the baking tunnel for this purpose. The measured values for each zone can be read both on the central control panel (touch panel) and moisture instrument.
6. In the event of a driving motor failure, the belt can be driven by the hand device. This could send the product out of the oven.
7. OMRON PLC system is built into the control cabinet for the control of the oven.
Suction Depanner/ Needle Depanner/ push-bar depanner
By means of a pick-and-place principle, a depanning head is positioned above pans; the (exchangeable) depanning head picks up the product and then transfers it to the cooling conveyor and releases it.
Edge pan cooler
Spiral cooler